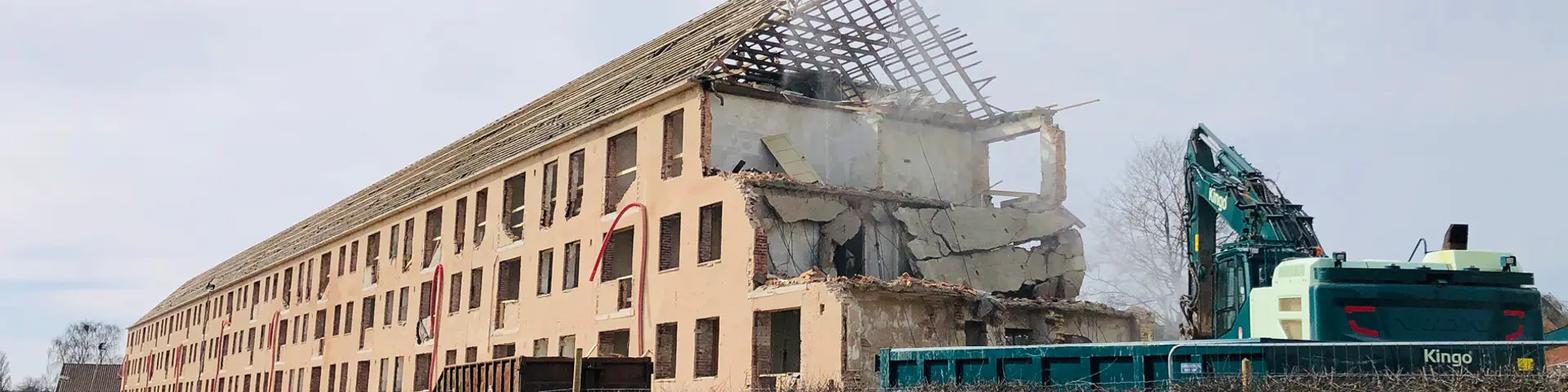
- Frontpage
- · Demolition
- · Demolition process
HOW TO SUCCESSFULLY NAVIGATE THROUGH THE DEMOLITION PROCESS
There are a variety of factors before, during, and after demolition that you need to be aware of.
Environmentally hazardous substances must be located, and demolition materials must be sorted and reused or recycled as much as possible.
There needs to be full traceability of the materials and waste from the completed demolition. Therefore, documentation must be provided for the disposal of hazardous substances as well as documentation for where the clean materials have been reused or recycled.
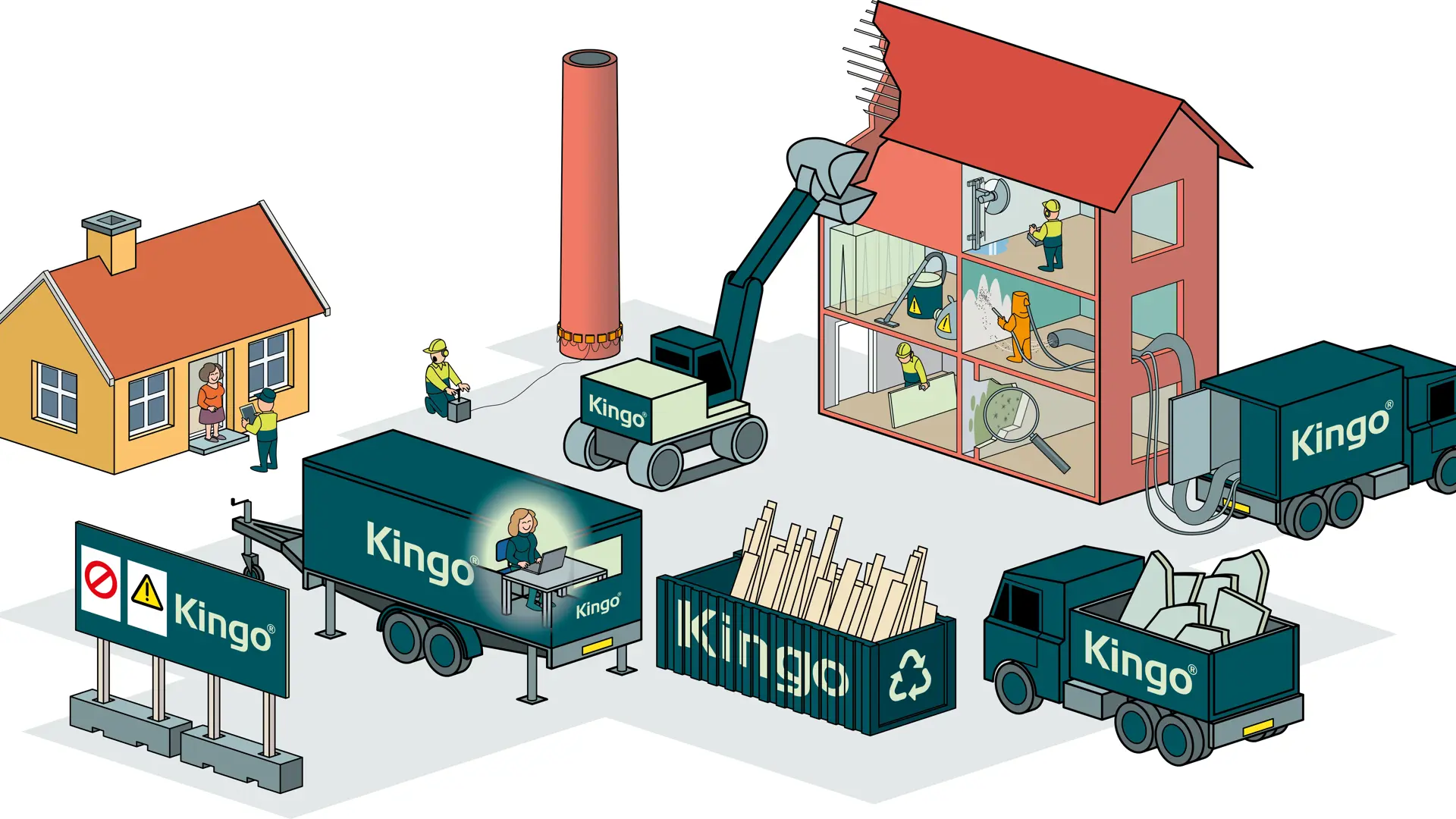
BEFORE DEMOLITION
If you are the developer or owner of the building, you must ensure the following before demolition:
- Obtain a demolition permit from the municipality. You can also authorize a consultant or demolition company to obtain the permit for you.
- It is your responsibility to ensure that the buildings are screened and mapped for environmentally hazardous substances (PCB, asbestos, heavy metals, etc.). You can have this task carried out by a consultant with specialized knowledge in mappings. Remember - this is an absolute condition in the demolition permit. For smaller projects, the demolition company can handle the mapping.
- Ensure that the waste is reported to the local waste authorities. You can ask the demolition company to show you the notifications.
- If there are more than 10 employees on the site at a time from more than one company, you as the developer must appoint a health and safety coordinator and prepare a safety and health plan (PSS). This plan should evaluate risk factors in the demolition.
- Once you have a screening or environmental assessment, you can obtain a price quote from a demolition company. We recommend that you get quotes from a company that can demonstrate experience in responsible demolition and provide necessary proof of education in environmental remediation and demolition.
- You must clarify the scope of the work with the demolition company.
- Together with the demolition company, review the offer so that all questions are clarified, and you can place a final order for the demolition.
- Hold a kickoff meeting to review the upcoming work and PSS.
The selected demolition company must do the following before starting the work:
- Appoint a project manager who will be your main contact throughout the process. The project manager plans resources and creates a detailed plan for the process.
- Prepare a quality, safety, and environmental plan (QSE plan) that follows the demolition.
- Ensure that the waste is reported or, if agreed, self-report the waste to the authorities, who direct the waste to appropriate recipients.
- Declare the waste to the various receiving sites. Without declarations, the demolition company or carrier cannot dispose of the waste.
- Retrieve information about underground pipes from the LER register. Schematics are received from the owners of the pipes and printed. They are given to the machine operator who will carry out the demolition and any excavation work.
- Notify the local environmental authorities of demolition and possibly crushing activities, who grant a temporary permit with conditions for the work. The conditions typically involve limiting environmental disturbances such as noise, vibrations, dust, and providing neighbours with information about any environmental disturbances during the temporary work period.
You can always ask the demolition company to provide documentation for the above.
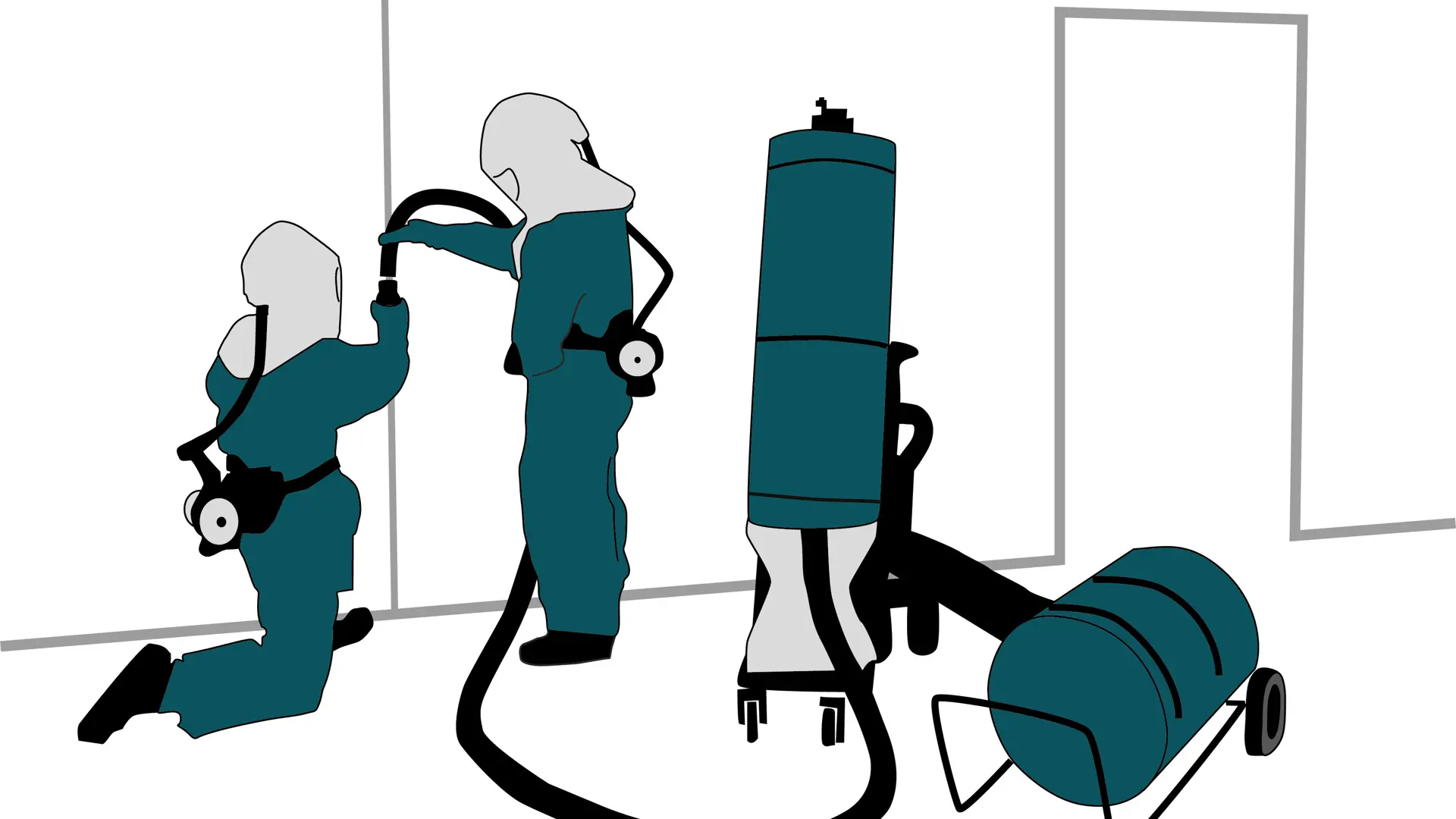
DURING DEMOLITION
- As the first step in the process, the demolition company removes all loose materials, furniture, etc.
- Following that, the demolition company performs environmental remediation of the building for the environmentally hazardous substances indicated in the environmental assessment.
- The demolition company must establish a remediation area with barriers and negative pressure ventilation. This ensures that environmentally hazardous substances are not spread to the surroundings during the remediation work.
- The environmentally hazardous substances are removed using the most optimal methods, which involve limiting waste and ensuring the safety and health of the workers.
- The environmentally hazardous waste is disposed of at an approved receiving site designated by the municipal waste authority. Traceability of all materials is ensured with digital transport documents and weighing slips.
- The remediation area is cleaned, and equipment is decontaminated.
Subsequently, selective demolition can be carried out.
- Clean materials are sorted for direct reuse or recycling, combustible materials are incinerated, and residual waste is sent to a landfill. This is often done through manual dismantling followed by demolition with hydraulic excavators equipped with sorting grabs and other tools.
- A portion of concrete and brick is reused today after cleaning in their original form. The concrete and brick that cannot be reused directly are crushed for recycling as a substitute for natural raw materials. The same applies to asphalt. For smaller projects, the materials are transported to environmentally approved crushing sites. For larger projects, crushing can occur on-site.
- The demolition is completed and delivered as agreed.
AFTER DEMOLITION
- The demolition company prepares a QSE report with documentation of the demolition processes, including proper disposal of waste quantities with full traceability. The report is sent to you as the developer.
- With the report, you have documentation that the demolition has been carried out in accordance with applicable regulations and can demonstrate full traceability for all demolished materials.
- All documentation from the demolition contract is archived by the demolition company for 5 years.
Watch the video where Kingo demolishes Vinkelgården in Frederikshavn:
A special task that started as an environmental remediation project but evolved into a complete demolition. Learn more about the project here.